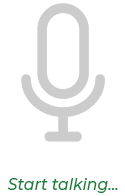
IFFCO’s Mother Plant
IFFCO’s first Urea & Ammonia production Facility, Kalol Production unit was commissioned in 1974 with a production capacity of 910 MTPD of Ammonia & 1200 MTPD of Urea. Over the last 4 decades, IFFCO Kalol Production unit has expanded & reinvented to stay at par with the modern production units both in terms of production capacity as well as the technology. Today IFFCO Kalol plant has a production capacity of 1100 MTPD of Ammonia and 1650 MTPD of Urea.
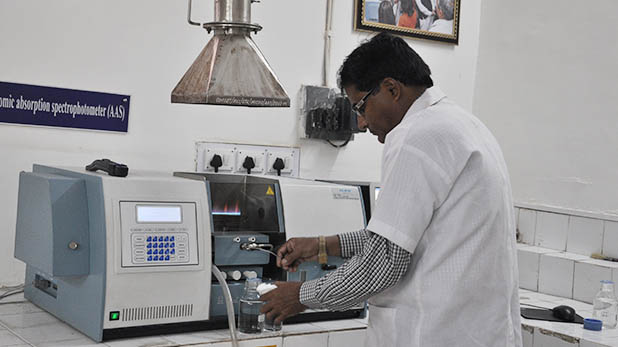
Production Capacity & Technology
IFFCO Kalol Plant is into its 40th year of production and is still one of the largest in terms of its production capacity
Products | Daily Production Capacity(Metric Ton Per Day (Metric Ton Per Day) |
Yearly Production Capacity(Metric Ton Per Annum) (Metric Ton Per Annumn) |
Technology |
Ammonia | 1100 | 363000 | Kellogg, USA |
Urea | 1650 | 544500 | Stamicarbon, Netherland |
Production Trends
Energy Trends
Plant Head
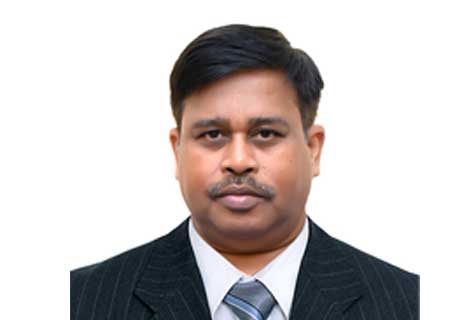
Mr.Sandeep Ghosh Executive Director
Mr. Sandeep Ghosh is a Chemical Engineering graduate from the University of Jadavpur. He joined IFFCO Kalol Unit as a graduate engineer in 1988.His experience spans 36 years, from production management, project conception to commissioning of Ammonia & Urea plants at IFFCO Kalol. He has held several key positions at IFFCO in the past which includes his stint as Project Head of NFP-II project and Unit Head of Nano Fertiliser Plant at Kalol. Currently, he holds the position of Executive Director and heads the Kalol Unit.
Awards & Accolades
Certifications
Kalol Unit boasts of the following certifications:
- ISO 50001:2011 for the Energy Management System (EMS).
- Integrated Management System (IMS) consisting of Quality Management System (ISO 9001:2015)
- Environment Management System (ISO 14001:2015)
- Occupational Health and Safety Management System (OHSAS 18001:2007)
- Kasturinagar Township for Environment Management System (ISO 14001:2015) and under Green Residential Society Rating System of Indian Green Building Council (IGBC) under the platinum category
Compliance Reports
Six monthly reports on status of compliance of EC Conditions
Other Initiative
Energy Saving Project (ESP) at Kalol
A number of upgrades & schemes have been implemented at the Kalol plant recently (2016 – 18) in an effort to make it more energy efficient:
Ammonia Plant
- New Secondary Reformer Burner.
- Liner Replacement of primary waste heat boilers (101-CA/B) with improved material of construction (MOC).
- Hydro De-Sulphurization of feed gas in place of activated carbon.
- New Process Air-Steam Coil with improved Material of construction (MOC).
- New single steam turbine (103-JT) for Syn Gas Compressor in place of two turbines.
- New Methanator Exit Cooler (115-C) with better design.
- MP Process Condensate Stripper in place LP Process condensate Stripper.
- Ammonia recovery from Syn Loop of LP Flash off gases.
- New Low Temperature HP steam superheat coil with higher area for better heat recovery.
Urea Plant
- High Efficiency Tray (HET) in Urea Reactor.
- VAM package for CO2 cooling.
- New CO2 Cooler in place of direct contact cooler.
- HP Ammonia Preheater (H 1250).
- HP Split Flow Loop and New High Pressure Carbamate Condenser (HPCC).
- HP Carbamate Ejector in HP Loop.
- New Second stage Evaporator Heat Exchanger with higher area.
Expansion Project phase II
one-Ammonia-Urea complex along with associated Offsite/Utilities & captive power plant to meet the requirement of whole complex.