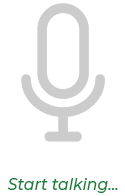
Championing Sustainable Development
IFFCO Aonla manufactures Ammonia and Urea and houses two production units having a combined installed capacity of 3480 MTPD of Ammonia and 6060 MTPD of Urea. IFFCO Aonla Unit has been at the forefront of sustainable production, adopting the most stringent measures to maintain the ecological balance. The Unit is spread across 694.5 Acres.
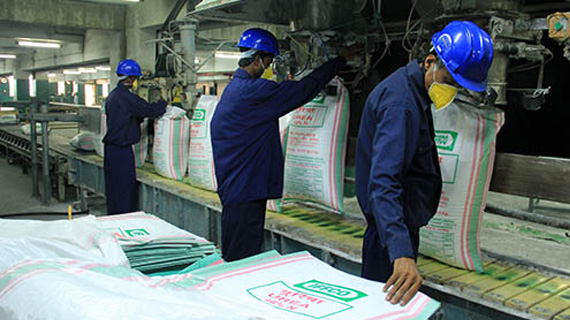
Production Capacity & Technology
Products | Daily Production Capacity(Metric Ton Per Day) | Yearly Production Capacity(Metric Ton Per Annum) | Technology |
Aonla-I Unit | |||
Ammonia | 1740 | 5,74,200 | Haldor Topsoe, Denmark |
Urea | 3030 | 9,99,900 | Snamprogetti, Italy |
Aonla-II Unit | |||
Ammonia | 1740 | 5,74,200 | Haldor Topsoe, Denmark |
Urea | 3030 | 9,99,900 | Snamprogetti, Italy |
Production Trends
Energy Trends
Production Trends
Energy Trends
Plant Head
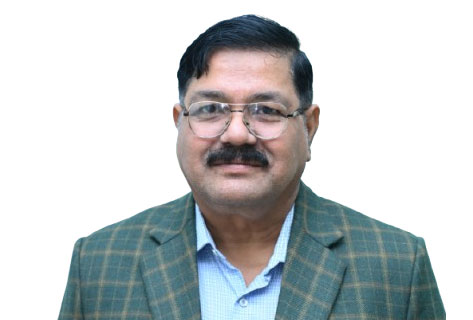
Mr. Satyajit Pradhan Sr. General Manager
Senior General Manager Shri Satyajit Pradhan is currently the head of IFFCO Amla unit.
During his vast experience of 35 years in Aonla Unit Plant, Engineer Mr. Satyajeet Pradhan has executed various work projects in Oman (OMIFCO) Plant from 20th September 2004 to 21st October 2006.
Engineer Satyajit Pradhan, who started his career as Graduate Engineer Trainee on 28th November 1989, is a professional and experienced Chemical Engineer.
Compliance Reports
The copy of Environment Clearance granted for the project “Modernization of Nano Fertilizer Plant, Aonla Unit at IFFCO Aonla
2024-02-05Six monthly compliance status report of project “Modernization of Nano Fertilizer Plant, Aonla Unit at IFFCO Aonla” April 2024 to September 2024.
2024-07-12The Environmental statement for financial year 2023-24
2024-23-09